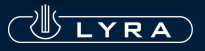
LYRA ETNA Lambda MONO

LYRA ETNA MONO Lambda monophonic “New Angle”
This is a special, built-to-order, mono version of Etna for real mono playback of monaural/monophonic (mono) microgroove, vinyl records. It is recommended that the Etna Mono is used with high-gain, low noise phono stages, or alternatively a step-up transformer designed for phono cartridges of 2 – 3 ohms or less. On mono records, the vertical axis of the groove contains no musical information, but it will frequently have noise, in the form of groove damage and dirt. The Etna Mono has therefore been designed to be completely insensitive to the vertical axis, which greatly improves the signal/noise ratio without any downside on monaural records. The coil former is a square permeable plate oriented parallel to the record surface rather than the 45-degree angle used for most stereo cartridges, while the coils are wound so that they only generate a signal when there is horizontal movement of the stylus and cantilever when tracking a record. Two totally separate monaural coils are used in the Etna Mono, since most monaural cartridges are used with stereo amplifiers and stereo speakers. The separate coils also help avoid possible ground loops and hum problems that could otherwise be caused if a single coil is fed into a stereo two-channel amplification system, thereby tying the two channels together electrically. In addition to parallel mono connection to a stereo system (two amplifiers and two speakers), it is also possible to leave one set of connections unattached for pure mono playback with a single amplifier and a single speaker. However, it is also possible to connect the two mono channels in series for additional output when used in a pure mono system. Use a short cartridge headshell lead wire with female pin-connectors to connect either the Etna Mono’s upper right pin with the lower left pin, or alternatively the upper left pin with the lower right pin. Then use the two remaining unused pins for connection to your single amp RIAA input (alternatively a transformer input). The two internal channels are now “chained” in serial-connection for additional output and energy when you only use a single amplifier and a single speaker. SPECIFICATIONS FOR ETNA MONO • Designer: Jonathan Carr • Builder: Yoshinori Mishima (final build, testing), Akiko Ishiyama (preliminary build) • Type: Medium weight, medium compliance, low-impedance, low-output moving coil cartridge • Stylus: Lyra-designed long-footprint variable-radius line-contact nude diamond (3um x 70um profile, block dimensions 0.08 x 0.12 x 0.5mm), slot-mounted • Cantilever system: Diamond-coated solid boron rod with short one-point wire suspension, directly mounted into cartridge body via high-pressure knife-edge system • Coils: Two individually isolated monophonic/monaural 6N high-purity copper coils wound in parallel (on top of each other) on a square-shaped chemically-purified high-purity iron former with 3.0 ohms self-impedance • Output voltage: 0.25mV@5cm/sec., 2.4μH inductance • Frequency range: 10 Hz-50 kHz • Channel separation: 35 dB or better at 1 kHz • Compliance: Approx. 12×10-6cm/dyne at 100Hz • Vertical tracking angle: 20 degrees • Cartridge body: Multi-material (titanium, duralumin, bronze, stainless steel) self-clamping construction with reduced-surface higher-pressure headshell contact area, predominately non-parallel shaping, phase-interference resonance-controlling mechanisms, body threaded for mounting screws • Cartridge mounting screws: 2.6 mm 0.45 pitch JIS standard • Distance from mounting holes to stylus tip: 9.5mm • Cartridge weight (without stylus cover): 9.2g • Recommended tracking force: 1.65 ~ 1.78g (1.72g recommended) • Recommended load directly into MC phono input: Determine by listening, • Recommended load via step-up transformer: Use a step-up transformer designed for 2 – 3 ohms cartridge impedance. The transformer output must be connected to standard 47kohm MM-level RIAA input, preferably via short, low-capacitance cable • Recommended tonearms: High-quality pivoted or linear tangential tonearms with rigid bearing(s), adjustable anti-skating force, preferably VTA |
Les technologies LYRA :
La nouvelle cellule LYRA ETNA partage son nom avec le majestueux volcan de Sicile. Elle impressionne en effet à plus d’un titre, en alliant les toutes dernières trouvailles du concepteur des cellules phono LYRA, Jonathan Carr, aux principes éprouvés développés pour les modèles précédents.
Le cœur de l’ETNA est en titane massif, mais, contrairement au haut de gamme Atlas (et auparavant à la Titan-I), ce noyau central est entouré par une coque externe usinée dans un aluminium de qualité aéronautique hautement poli et anodisé avec une finition noire attrayante. Les deux pièces sont assemblées par pressage (pas de colle) avec des barres antirésonance et trous traversants pour les vis en acier inoxydable amagnétiques. Cette approche est similaire à celle de la Skala mais avec une rigidité et des caractéristiques d’amortissement mécanique très supérieures. L’avantage de cette construction multi-matériaux et multicouche est qu’à la différence de l’usage d’un matériau unique, aucune signature sonore répétitive n’est perceptible ; il n’y a pas de coloration permanente perturbant la reproduction.
La construction de l’ETNA emploie une armature de forme asymétrique, différente à droite et à gauche. Ce concept de construction qui a fait ses preuves avec l’ATLAS. En décalant le support frontal de l’aimant de telle sorte qu’il ne soit pas aligné avec le levier porte diamant, un chemin direct est créé entre celui-ci et le bras de lecture. Les vibrations s’écoulent rapidement une fois converties en signaux électriques, supprimant efficacement toute résonance induite, génératrice de coloration sonore. LYRA reste le seul fabricant de cellules à monter le levier porte diamant directement dans le corps de la cellule créant ainsi une liaison continue totalement rigide entre le levier porte diamant et la coquille. Le levier porte diamant lui-même est en bore plaqué diamant et équipé d’un diamant « fine line contact ».
L’ETNA conserve la disposition en X des bobines, d’abord dévoilée dans l’ATLAS. Comparée à la disposition en carré traditionnelle, la forme en X permet à chaque canal de travailler indépendamment de l’autre, augmentant la cohérence de la lecture de chacun tout en améliorant aussi la séparation des canaux en raison de la diminution de diaphonie.
Comme la Delos, la Kleos et l’Atlas, l’’ETNA utilise la nouvelle technologie « les vinyles sous un autre angle ». L’axe des bobines mobiles est incliné au repos de telle sorte qu’elles sont parfaitement alignées avec les aimants avant et arrière pendant la lecture des LP (la force d’appuis modifiant l’alignement du porte diamant). Grace à cette disposition originale, les bobines mobiles se déplacent de manière optimale dans toutes les directions et dans un champ magnétique uniforme. Les distorsions de lecture sont minimisées.
LYRA ETNA Lambda “New Angle”, “Asymmetric”, “Multi-Material”
It is always a challenge to design a worthy heir to a successful product. For the Lyra Etna, however, that challenge was twice as difficult as normal. On one hand its primary goal was to replace the popular Titan. On the other hand, the Etna design project had a second goal, which was to achieve as high levels of performance as possible. If this meant that Etna would give stern competition to the flagship Atlas, so be it. As a model intended to retail for significantly less than Atlas, but having similar aspirations to the pinnacles of performance, Etna was designed with a strong emphasis on engineering efficiency, so that its performance would be as far beyond the sum of its parts as possible. For this reason, although it shares some of its design philosophy with the Atlas, the concepts are executed rather differently. Etna employs a solid titanium core structure machined with non-parallel surfaces to inhibit internal reflections wherever possible, but unlike Atlas (and Titan i before it), this is mated to a slightly undersized, asymmetric duralumin outer body that is designed to lock over the core like a very tightly-fitting jigsaw puzzle. The core and body are augmented with bronze and stainless-steel resonance control rods, then everything is pressure-fit together into a pre-stressed, solid, void-free structure which is comprised of multiple materials and complex internal shapes. The constrained-layer nature of this construction dramatically reduces the resonant signature of each material and creates a far more neutral-sounding body structure than otherwise possible, while the high body stiffness benefits transients, dynamics and resolution. Linear transducers such as loudspeakers and phono cartridges are inherently inefficient devices – on the order of 5 to 10%. In other words, of the vibrational energy that enters a cartridge from the LP groove, only 5 to 10% will be converted into electrical signal. The cartridge’s internal damping system will dissipate some of the remaining 90 to 95%, but much of the excess vibrational energy will reflect inside the cartridge, creating internal echoes, smearing, and a general diminishing of fidelity. It is easy to demonstrate this with many cartridges – play a highly modulated LP with the power amp turned off, and bring your ear close to the cartridge. The “needle-talk” that you hear is excess vibrational energy which isn’t being controlled properly. To help conduct this excess vibrational energy into the headshell, where it can be safely dissipated within the greater mass of the tonearm and turntable plinth, Lyra has traditionally mounted the cantilever directly into the cartridge body, resulting in a rigid, seamless connection between the cantilever assembly and tonearm headshell (as it happens, we remain the only manufacturer to do so). In the process of designing Atlas, we discovered that in addition to coupling the cantilever to headshell with a rigid, unbroken path, further sonic gains could be realized by removing all objects and voids from the path. Atlas’ asymmetric shape was conceived partly for this purpose, to move the front magnet carrier, mounting screw and screw hole out of the way of the mechanical path connecting cantilever to headshell. Etna utilizes the same asymmetrical concept, but whereas Atlas offsets the screw and screw hole to one side, Etna moves the screw / screw hole all the way to the front of the cartridge – and interposes an additional bronze damping barrier between the screw / screw hole and the mechanical path linking cantilever to headshell. By displacing the front magnet carrier and other components so that no objects or voids are in line with the cantilever assembly, a truly direct path is established between the cantilever assembly and headshell. Control over spurious resonances is further assisted by the use of a narrowed mounting area, which couples Etna more tightly to the headshell and facilitates the transfer of vibrational energy into the tonearm. Vibrations are quickly drained away once converted to electrical signals, effectively suppressing induced resonances and internal reflections that would otherwise manifest themselves as sonic colorations and overhang. Etna uses a yokeless dual magnet system, diamond-coated boron rod cantilever and Lyra-designed variable-radius line-contact stylus (major radius 70 micrometers, minor radius 3 micrometers, block dimensions 0.08 x 0.12 x 0.5mm, mounted within a slot machined into the front of the cantilever), and builds the cantilever assembly directly into the titanium body structure. Both the cantilever and the insides of the titanium body core are shaped so that joining the two components to each other creates a double-knife-edge mounting system, which focuses as much pressure as possible on the joint area and achieves a type of cold weld. More rigid than the cantilever mounting system employed in the Titan, this design facilitates the transfer of mechanical energy away from the stylus and signal coil area and minimizes reflected mechanical energy, thereby significantly reducing distortion and resonances. Another design strength is Etna’s high-efficiency X-shaped signal coils, which it shares with the flagship Atlas. Compared to traditional square coil formers the X-shape allows each channel to operate with greater independence from one another, giving better tracking, tighter channel matching, improved separation, and lower crosstalk-induced distortion. Although there are and have been other X-coil cartridges; their benefits have been accompanied by poor efficiency (in converting mechanical work into electrical output), either requiring high internal impedance (the larger coils add considerable moving mass and increase noise), and/or having low output voltage (which stresses the phono stage). To overcome this weakness, Lyra conducted a careful investigation of X-core coils, using a combination of mathematical analysis and hands-on experimentation. The outcome of the analysis program was a very specific X-core shape that not only had higher efficiency than any previous X-core cartridge, but also surpassed the efficiency of our earlier square-coil cartridge designs. Rather than using all of the extra efficiency to single-mindedly increase the output voltage, we chose to allocate part of the extra efficiency to increase the output voltage (12% higher than Titan i), and use the remainder of the extra efficiency to reduce the amount of wire in the coils (22% less than Titan i). The lowered mass further improves tracking performance, while the higher output and lower internal impedance allow phono stages to perform better. Etna uses Lyra’s “New Angle” technology, which mechanically pre-biases the signal coils so that the vertical tracking force brings them into perfect alignment with the front and rear magnets when LP playback takes place. This system also equalizes out discrepancies in vertical and horizontal compliances, and enables Etna’s coils to move with equal ease in all directions for wider dynamics, higher resolution, and improved tracking. In every possible way, we have done our utmost to enable Etna to reach the very highest levels of performance. While Etna is second from the top in Lyra’s line, one listen will demonstrate that its performance would define the very top of any other cartridge line. |